KEENPRO PASSED THE SGS CERTIFICATION POWER SAVING MECHANISM
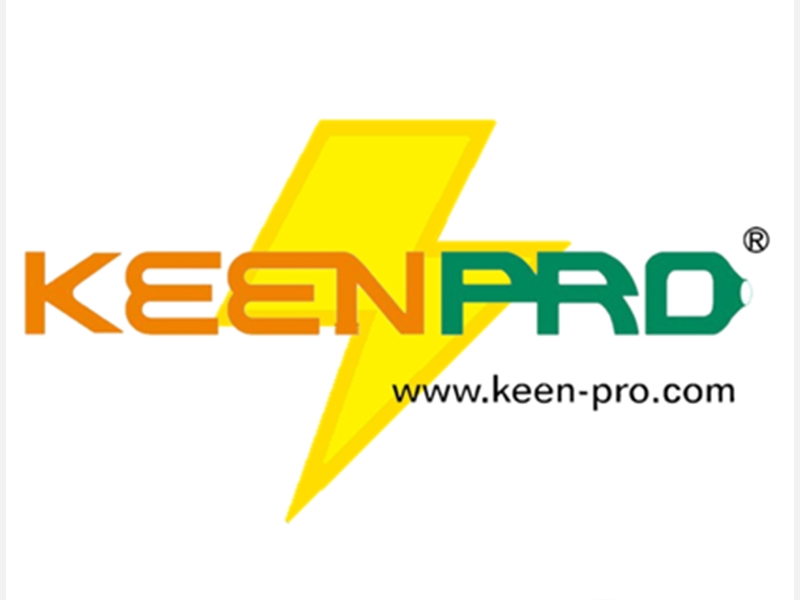
KEENPRO designed the machine structure with power saving as the starting point, and the requirements of energy-saving and high-efficiency equipment are getting higher. The development trend of this industry is still towards environmental protection, energy-saving, lightweight, high-speed, automation, intelligent direction, we had been through all of these. In 2019, KEENPRO also completed SGS power testing, which is divided into conversions by four blow molding machines in a similar product specification production line. The test results are shown in the following table.
.jpg)
The EM series overcomes the weaknesses of the traditional heating method and adopts the method of concentrated heating and reflection heat collecting at both sides of the single lamp tube to achieve full utilization of the lamp energy and reduce waste. Besides, in the gas circuit design, using the high-speed parallel valve body design and gas recovery circuit design, more than 45% recycling efficiency and also reduce machine's investment, and power consumption. Because of these innovative designs, TEM06S2, for example, saves 57.78kwh per 10,000, assuming a monthly production of 2 million bottles, converting 24 million bottles per year, and saving a total of 138,000KW per year, it shows a very competitive advantage.